The vast majority of manufacturing industries are still manually recording data and storing paper records and reports in filing cabinets or warehouses. Given the value of business data and the need to preserve it, the manufacturing sector could consider partnering with data entry companies to capture data and store it in digital format for easy access and retrieval.
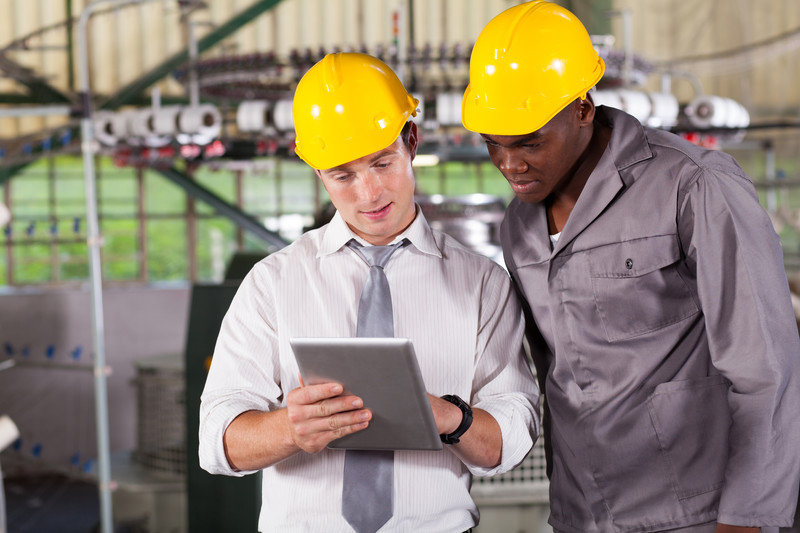
A recent survey by InfinityQS of 260 manufacturers found that 75% of respondents are still collecting data manually; 47% are using paper checklists. Even though manual data collection is more time-consuming, frustrating and highly vulnerable to human error and inaccuracies, many manufacturers continue using this method. This is due to the fear that changes might be difficult and expensive. Re-evaluating the data processes in the areas including collection, analysis and reporting, and updating the way to manage data in any of these categories can produce measurable and significant benefits which include fewer data errors, reduced scrap and waste, and faster reporting and response to audits.
Taking a Fresh Look at Data Processes in Three Areas
Data Collection
Paper-based data entry is more prone to error than automated data collection or digital data entry by operators. Measurements from scales or other equipment can be scribbled down, transcribed incorrectly or overlooked completely. Errors such as a simple math mistake or misread handwriting (Is that a 1 or a 7?) can lead to a domino effect of disastrous results. Furthermore, paper records can be easily lost in transport or forgotten in an ocean of filing cabinets. In addition to that, if data is being recorded on paper, the manufacturer may not be able to verify whether it has been collected properly and on time. It is also essential for operations and quality teams to have easy, fast access to real-time data, not data from hours ago that was written down on a piece of paper somewhere across the plant floor.
To overcome this issue, manufacturers should look for a real-time statistical process control (SPC)-enabled quality intelligence solution which supports automated and semi-automated data collection from a variety of equipment as well as tablet-based data entry for easy and efficient collection of non-automated data. The system should feature automatic alerts for scheduled data collections, thus letting operators know if collections are coming up or missed. In fact, scheduled and automated notifications can ensure timely and complete data collection, supporting compliance requirements and analysis needs. The system should also be smart enough to prevent data entry errors and identify data values that are out-of-specification.
Companies that use a real-time SPC solution to move away from paper-based data collection have started to see improvements in data integrity. This in turn helps companies reduce errors, improve compliance and catch violations more quickly before a problematic process affects the product.
Data Analysis
Operations and quality managers will have to spend hours and hours manually importing data into spreadsheets or other external software and subsequently performing data manipulation to compare data with different targets and tolerances. In fact, most systems simply layer a database structure over an old-fashioned flat-file way of storing data; this makes it impossible to compare multiple products, lines, or sites on the same chart as well as limits the quality team’s ability to explore the types of details and comparisons that can transform a business.
- With a real-time SPC system, manufacturers do not have to find the data to put into a chart. Instead, they can simply query the software to get the information they need in the best format for analysis.
- The system also surfaces and filters the most important and relevant data, according to a specific user’s role and their defined priorities.
- It allows users to study the details and helps them to easily compare data across products, lines, processes, lots, shifts, operators, time, departments and sites, eliminating the need to switch back and forth between spreadsheets.
The SPC software can automatically provide extensive, easily readable views of the quality data including multiple chart types, reports, dashboards, and notifications, allowing operations and quality teams to save valuable time, while easily identifying the areas that are most in need of attention and prioritize the opportunities for reducing costs. It eliminates the need to dig through data or travel to the shop floor to find the information that is required by the operations team in real time. It also helps quality team to run analyses and comparisons of any and all data, without hours of manual spreadsheet or software manipulation.
Data Reporting
Manufacturers record real-time data on paper and store them in filing cabinets. However, when an audit takes place, it will be really difficult to locate these data, especially if they are stored in multiple locations for weeks, or months. The organization could even struggle to compile data from multiple locations and formats in response to customer inquiries, audits or executive needs.
A centralized Unified Data Repository within a quality intelligence solution automates and standardizes data storage. This makes it easy to access the information and also, data won’t get lost and may not be difficult to find. This will help save time when it comes to audits. Its ability to easily locate and access data from any day and time eliminates the need to sort through piles of paper or multiple spreadsheets, making audit preparation much less distressing. It makes it easy for the staff to find the right data (stored automatically and digitally in the repository) within a matter of minutes and provide exactly what an auditor requests. This in turn helps to focus and streamline the information-return process and avert costly delays and distractions.
Traceability improves with the ability to see process data from any point in time, including details about raw materials, shifts and operators, specific lines, equipment and processes. As everyone can access the same data, communications will be easier and more efficient. Since the quality teams can find the right answers with just a few clicks, this will help them to respond more quickly and precisely to customer inquiries.
Good quality data is important for all businesses to function smoothly and provide optimum customer service. This holds true for the manufacturing sector as well. The first step in ensuring reliable and accurate data is digitization of data residing in paper format. Using advanced technology including document scanning software and OCR Scanning, a reliable data entry company can help collect, arrange, organize and store valuable business information in electronic format.